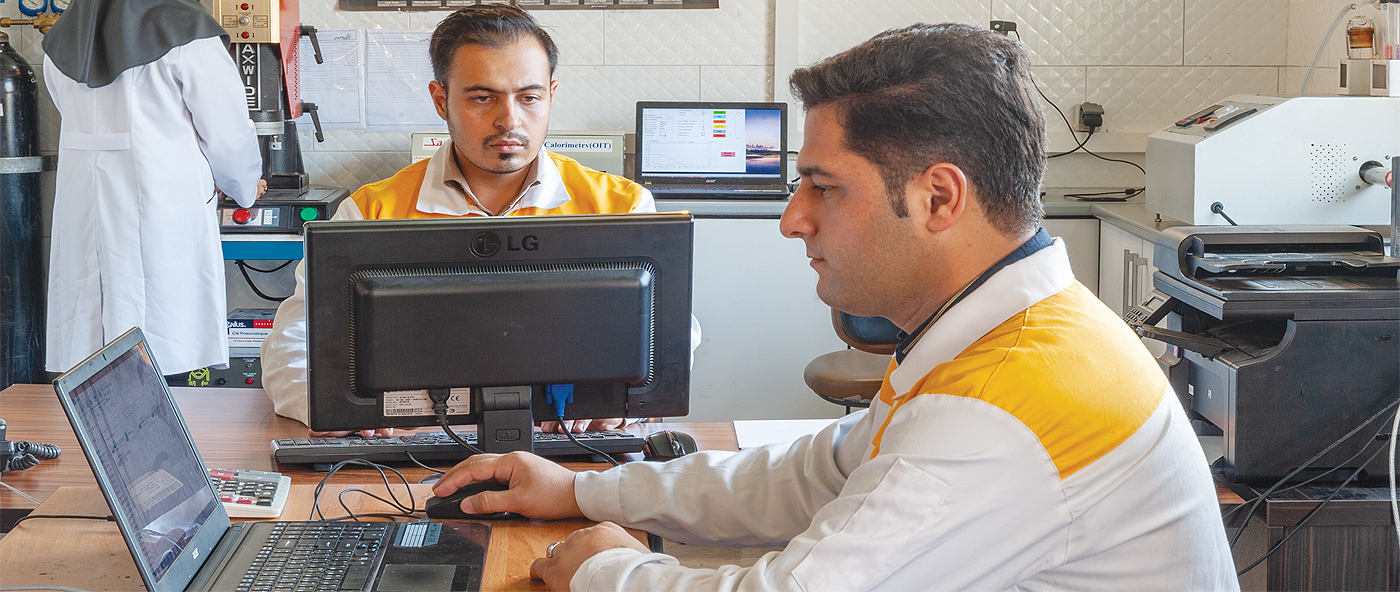
It’s a well known fact that only dynamism and development can put a manufacturer on the path to success. The global polymer pipe and fitting industry strives to improve the quality and efficiency of its products with easier installation. Hence, like a beating heart, the research and development, laboratory, and quality control departments should deliver blood and revitalize this manufacturer’s organs. The laboratory is calibrated according to the latest findings and works in standard conditions while utilizing the latest equipment from respected brands. After this short introduction, some of the features and objectives of the laboratory and quality control departments are briefly presented.
- Pipe and fitting visual inspection equipment (dimensional measurements)
- Melt flow index (MFI)
- Determination of density
- Determination of carbon content
- Carbon black dispersion test
- Tensile test
- Hydrostatic pressure test
- Fracture test
- Thermal response test
- Oxidation induction time (OIT) test
- Bearing test
- Environmental Stress-Cracking Resistance (ESCR) test
- Determination of volatile matters
- Determination of ring stiffness
Melt Flow Index (MFI) (ISO1133)
MFI is a practical measure of polymer flow rate and thermoplastic polymer viscosity in specific temperatures and pressures. It is also a function of polymer molecular weight. Specifically, MFT is the mass of a thermoplastic polymer (grams) that passes an 8 mm-long capillary with 2.0955 mm diameter in ten minutes due to pressure from a specific weight at a specific temperature. It is measured using a plastometer, and different standard MFI values are specified for different polyethylene types (LDPE, MDPE, HDPE).
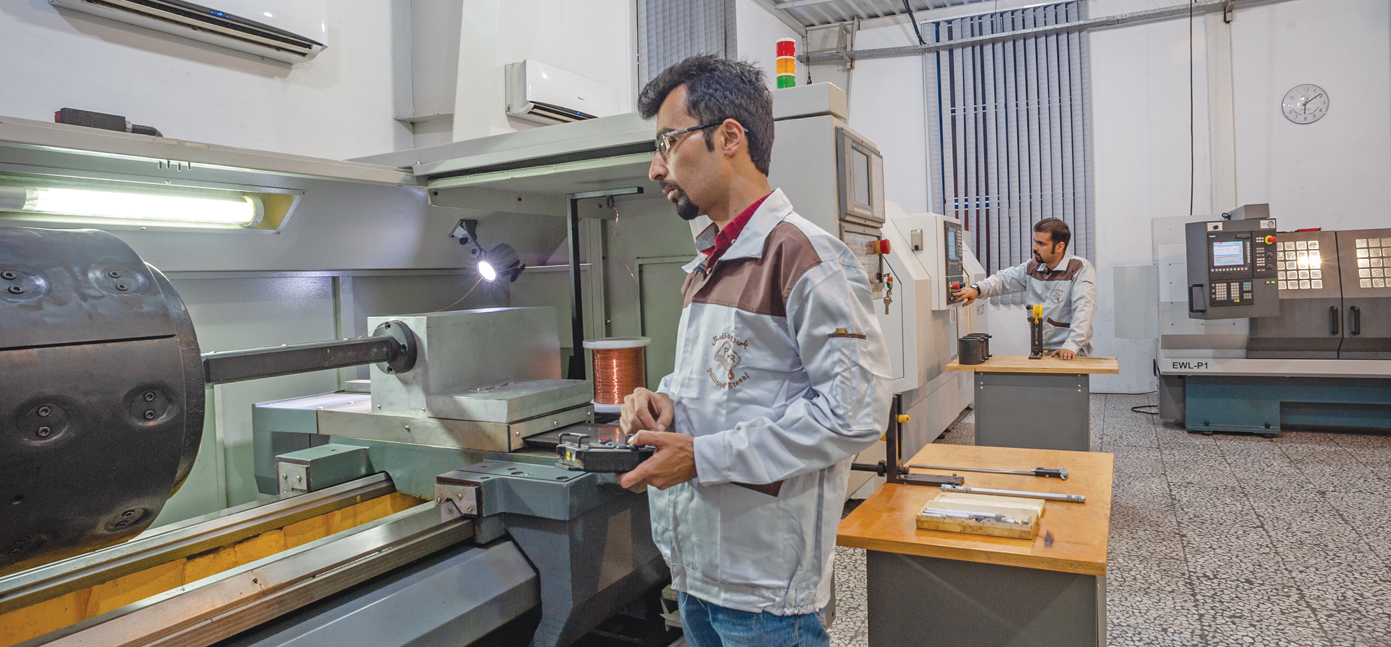
This test is for raw materials (quality check) and products, and standard product MFT should not exceed the raw material MFT by over 25%. Otherwise, the manufacturing process will require adjustments.
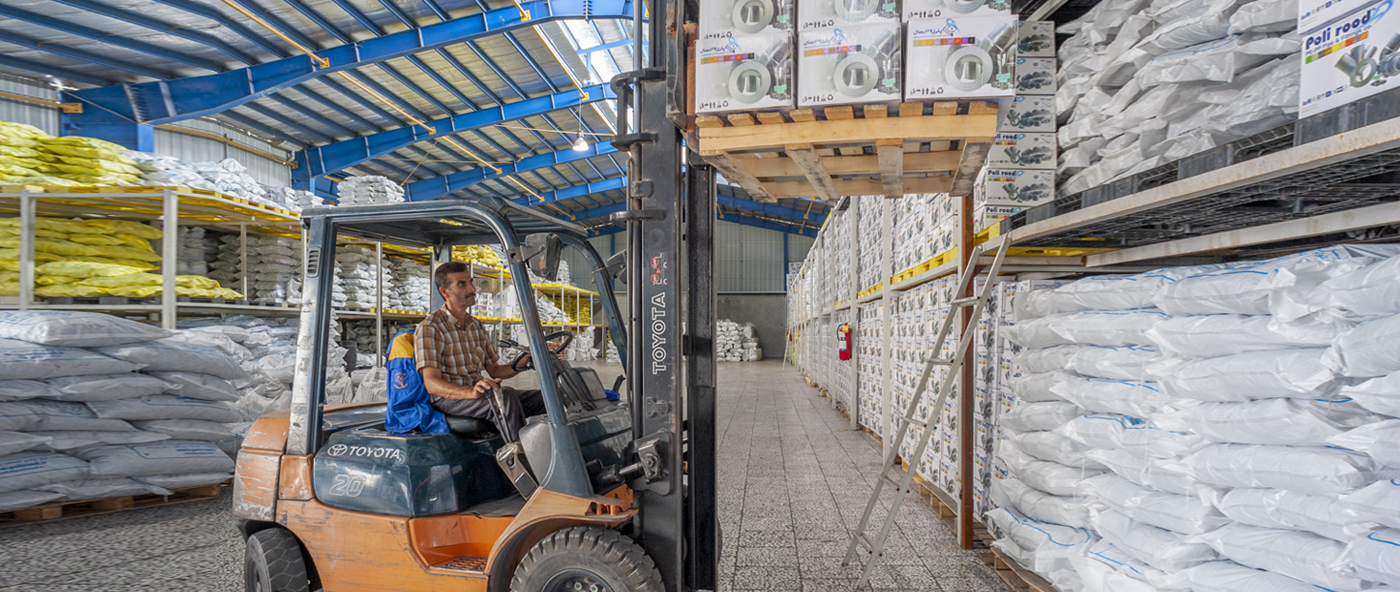
Determination of Density (ISO1183)
The density of purchased raw materials and products is determined with an accurate scale through floating and a fluid with a specific density. Product density represents the quality of the manufacturing process.
Determination of Carbon Black Content (ASTMD1603)
Carbon black is among the most important polyethylene additives for strengthening pipes against invasive atmospheric factors, especially UV radiation. Carbon black content is measured through pyrolysis using an electric furnace.
To this end, a specific amount of raw material is pyrolyzed in an 800 °C furnace under pure nitrogen gas and the remaining carbon content is burned under oxygen, thus allowing to measure the ash content (additives) of the initial sample. The acceptable carbon content for polyethylene pipes is 2 to 2.5 wt% and should be evenly distributed or, otherwise, tension will be concentrated in areas with excessive carbon content, making the pipe fragile. On the other hand, too little carbon content will reduce UV radiation resistance.
Hydrostatic Pressure Test (EN-921)
Hydrostatic pressure is the pressure applied to pipes in a specific time and temperature. Product hydrostatic pressure resistance is measured using the newly-imported IPT (the best and most accurate hydrostatic tester) equipment from Germany in the Polirood laboratory and research and production department. This test is conducted in two ways:
A) Short test: The sample is floated in a 20 °C water pit for 100 hours under constant pressure, after which no cracks, failures, protuberance, or defects should be observed.
B) Long test: The sample is evaluated according to the ISIRI1331 standard, where it is put under pressure and 80 °C temperature for 165 hours. Afterwards, no cracks, fracture, bagginess, local protuberance, leakage, hair cracks, or defects should be observed.
Fracture Pressure Test (ASTMD1599)
In this test, pipe samples are floated in a pit with a constant 20 °C temperature and placed under linearly increasing internal pressure to protuberate and crack in 60 to 70 seconds. High-quality fittings will initially change plastic shape and inflate with canary beak fractures. In this state, the fracture section is perpendicular to the pipe’s longitudinal axis.
Polirood’s laboratory is currently outfitted with the most accurate IPT hydrostatic pressure tester in Iran.
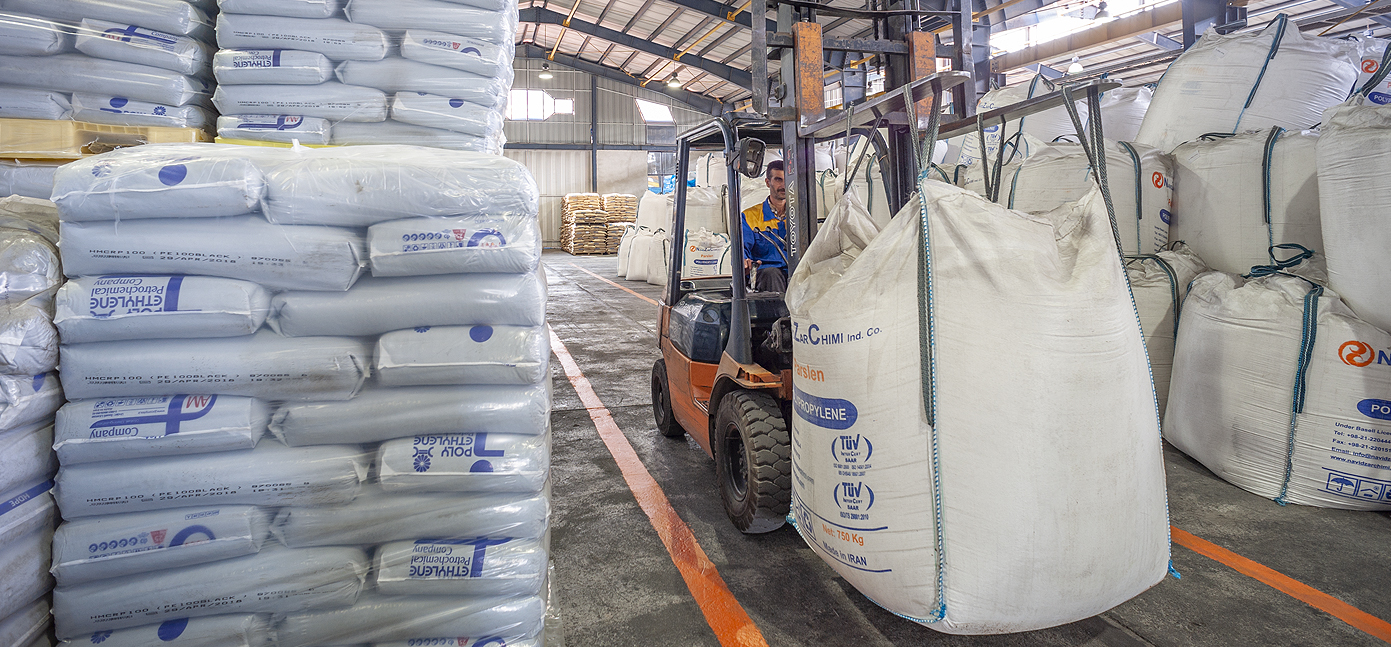
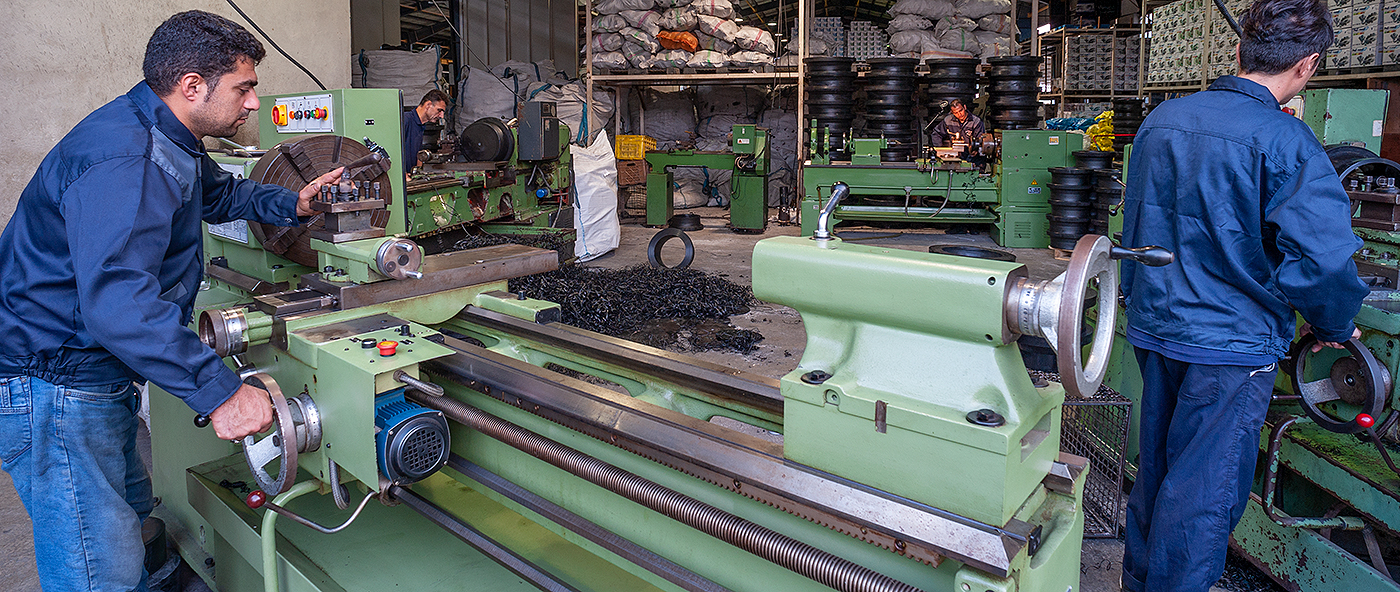
Thermal Response Test (ISO2502i)
Volumetric expansion coefficient is an important parameter for polyethylene pipes and fittings. Sudden environmental temperature changes always happen, and thermal fatigue, also known as thermal shock, is one of the worst factors to affect polymers. Therefore, the underground pipes that will withstand thermal shock due to water temperature changes should have low fatigue. Hence, their thermal response should be low to suffer less thermal fatigue damage.
In this test, samples with approximately 30 cm in length are placed in a hot air circulation (110 °C) oven for one to three hours (based on sample casing thickness), and length reduction after cooling will be calculated and compared to the initial length (length change as the percentage of initial length), which should not exceed 3% for 16 mm polyethylene pipes.
Dimensional Measurement and Visual Inspection of Pipes (ISIRI1333)
The sample’s external diameter, casing thickness, diameter variation in both ends (ovality), and pipe casing thickness range are quality characteristics that should be controlled with precision. The external diameter and casing thickness are respectively measured using a circometer and a digital caliper or micrometer. The samples’ internal and external surfaces should be flat and have no indentation or sharp edges. Minor inconsistencies and shallow depression can be ignored if they are within minimum casing thickness specifications.
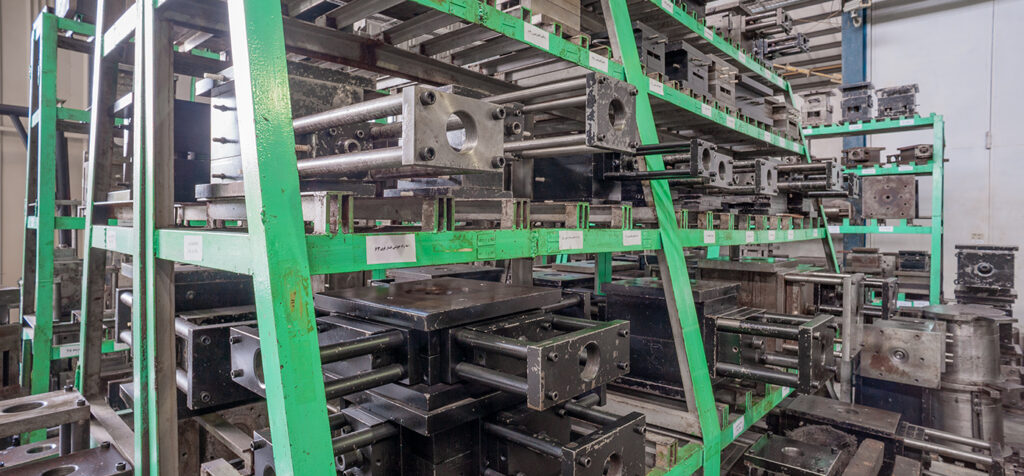
The ends of samples should be cut perpendicular to the axis as permitted. First, pipes should not have any protrusions or inconsistencies due to external materials that act as failure points and reduce pipe durability. The sample should have uniform color and no unpleasant smells.
Noncircularity or Ovality
The circular section deformation or ovality is measured according to the standard after production.
Due to their flexibility, polyethylene pipes and fittings change shape during storage, transportation, and installation, which is resolved by welding and fitting the pipe. Then, the pipe returns to its original shape after passing fluids and applying pressure.
We are proud to announce that Polirood Ettesal fittings are used throughout Iran and overseas.
Polirood Ettesal proudly welcomes you to this great family. Our representatives are ready to provide technical and business information and receive your recommendations and criticisms.